Cooper Base PCB
Name: Cooper-Base-PCB
Composition:
Composed of copper, insulating layer and copper foil, there are single-sided copper substrate and double-sided copper substrate.
Features:
✿ Stronger current-carrying capacity and better heat dissipation effect, thus ensuring the stability of the product.
✿ It has a strong withstand voltage value, does not contain heavy metal components, and has no pollution to the environment.
✿ Its products adopt SMT surface mount technology, which can effectively deal with heat dissipation in the circuit design scheme, does not require additional radiators, greatly reduces the volume, and greatly improves the mechanical processing performance of the product.
Process:
material cutting, drilling, line imaging, etching, silk screen solder mask, silk screen characters, surface treatment, CNC, withstand voltage test, etc.
What is the difference between copper substrate and aluminum substrate
✿ Physical properties
The thermal conductivity, electrical performance and processing performance of the copper substrate are all better than the aluminum substrate, and its thermal conductivity is as high as 400W/mK, which is much higher than the 200W/mK of the aluminum substrate.
✿ Application scenarios
Because the aluminum substrate has the characteristics of lightness, good heat dissipation and high strength, it is often used in LED lights or electronic equipment, mainly for heat dissipation. The copper substrate is usually used in high-speed circuits and high-energy circuits due to its strong thermal conductivity, which can effectively improve the performance and stability of the circuit.
✿ Processing technology
Aluminum substrates are relatively easy to process, and commonly used processing methods include laser cutting, drilling, and compounding. Copper substrates are relatively difficult to process. If you want to carry out processes such as line cutting, you need to use higher technology and equipment. However, the difficulty in processing also makes the copper substrate have a wider application space in some fields.
Therefore, you can decide what kind of circuit board to use according to the product requirements of your company.
Application: precision communication equipment and architectural decoration industry.
Due to its own characteristics, copper substrates cannot be replaced by aluminum substrates and FR-4 in some areas, as follows:
✿ The copper base can be etched with fine patterns and processed into a boss shape, and the components can be directly attached to the boss to achieve excellent grounding and heat dissipation.
✿ The copper base can be processed into metallized holes, but the aluminum base cannot. The network of metallized holes must be the same network, so that the signal has an excellent grounding function, and secondly, the copper itself has a solderable function, which makes the design of the structural parts later After all the device can be optionally soldered.
Because the hardness of copper is relatively large, there are not many thicknesses to choose from, only 1.0mm, 1.2mm, 1.5mm, 1.6mm, 2.0mm.
none

Composition:
Composed of copper, insulating layer and copper foil, there are single-sided copper substrate and double-sided copper substrate.
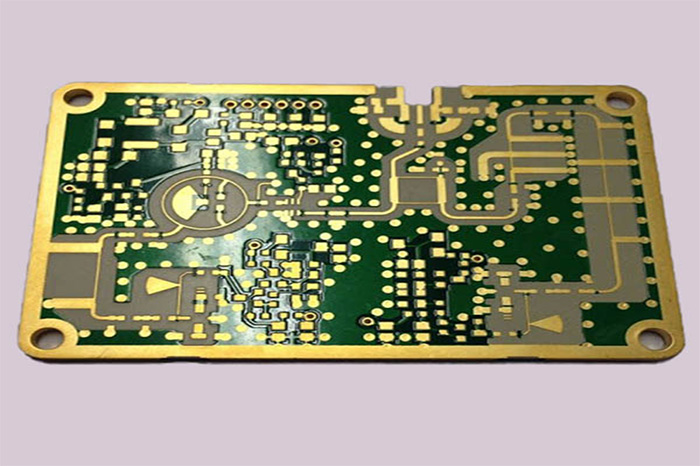
Features:
✿ Stronger current-carrying capacity and better heat dissipation effect, thus ensuring the stability of the product.
✿ It has a strong withstand voltage value, does not contain heavy metal components, and has no pollution to the environment.
✿ Its products adopt SMT surface mount technology, which can effectively deal with heat dissipation in the circuit design scheme, does not require additional radiators, greatly reduces the volume, and greatly improves the mechanical processing performance of the product.
Process:
material cutting, drilling, line imaging, etching, silk screen solder mask, silk screen characters, surface treatment, CNC, withstand voltage test, etc.
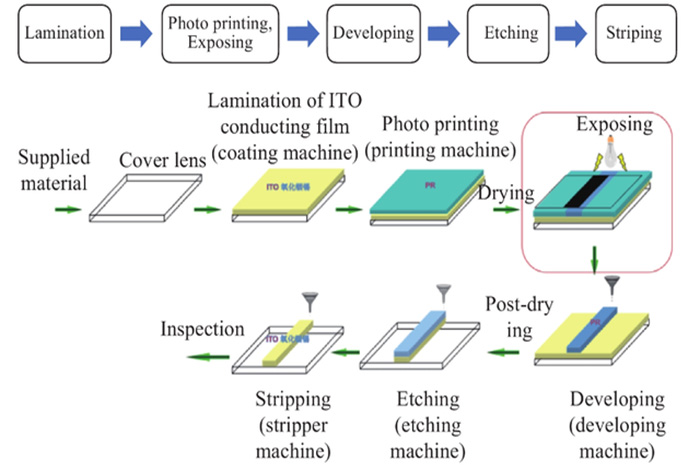
What is the difference between copper substrate and aluminum substrate
✿ Physical properties
The thermal conductivity, electrical performance and processing performance of the copper substrate are all better than the aluminum substrate, and its thermal conductivity is as high as 400W/mK, which is much higher than the 200W/mK of the aluminum substrate.
✿ Application scenarios
Because the aluminum substrate has the characteristics of lightness, good heat dissipation and high strength, it is often used in LED lights or electronic equipment, mainly for heat dissipation. The copper substrate is usually used in high-speed circuits and high-energy circuits due to its strong thermal conductivity, which can effectively improve the performance and stability of the circuit.
✿ Processing technology
Aluminum substrates are relatively easy to process, and commonly used processing methods include laser cutting, drilling, and compounding. Copper substrates are relatively difficult to process. If you want to carry out processes such as line cutting, you need to use higher technology and equipment. However, the difficulty in processing also makes the copper substrate have a wider application space in some fields.
Therefore, you can decide what kind of circuit board to use according to the product requirements of your company.
Application: precision communication equipment and architectural decoration industry.
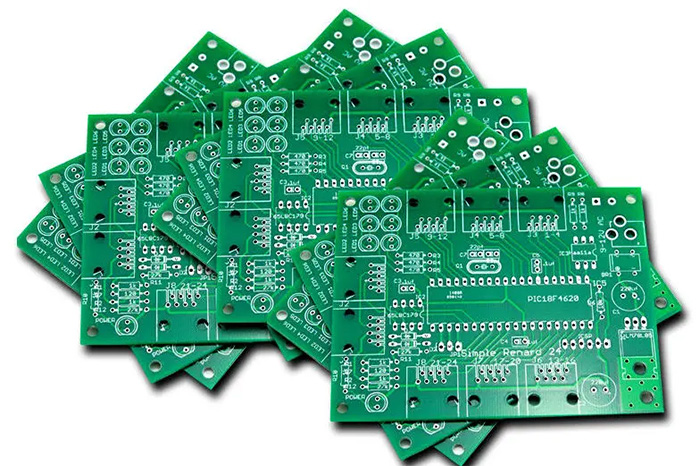
Due to its own characteristics, copper substrates cannot be replaced by aluminum substrates and FR-4 in some areas, as follows:
✿ The copper base can be etched with fine patterns and processed into a boss shape, and the components can be directly attached to the boss to achieve excellent grounding and heat dissipation.
✿ The copper base can be processed into metallized holes, but the aluminum base cannot. The network of metallized holes must be the same network, so that the signal has an excellent grounding function, and secondly, the copper itself has a solderable function, which makes the design of the structural parts later After all the device can be optionally soldered.
Because the hardness of copper is relatively large, there are not many thicknesses to choose from, only 1.0mm, 1.2mm, 1.5mm, 1.6mm, 2.0mm.